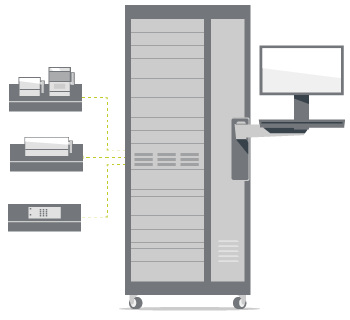
Erzielen neuer Testdimensionen
Bevor ein Testprojekt in Angriff genommen wird, ist es wichtig, ein Verständnis dafür zu entwickeln, wie rentabel die Investition sein wird. Wenn Sie verstehen, auf welchem Konzept automatisierte Tests, warum sie eingesetzt werden und wann sie verwendet werden sollten, ist die Frage nach der finanziellen Rechtfertigung im Wesentlichen beantwortet.
Erfolgreiche Produkttests sind entscheidend für die Qualität, aber sie haben selbstverständlich auch ihren Preis. Die Entscheidung, ob die Tests manuell, automatisch oder in einer Kombination aus beidem durchgeführt werden sollen, ist von vielen Faktoren abhängig. Entscheidungsträger müssen die wichtigsten Kostentreiber sowie moderne Best Practices verstehen.
Hier finden Sie Infos zu folgenden Themen:
Die Geschichte automatisierter Tests
Manuelle Tests im Vergleich zu automatisierten Tests
Typen automatisierter Tests
Entscheidung zwischen manuellen und automatisierten Tests:
Eignet sich das Anwendungsfeld für Automatisierung?
Ist die Automatisierung die finanzielle Investition wert?
Definition automatisierter Tests
Bei automatisierten Tests wird ein Computer in die Lage versetzt, eine Reihe von Einzeltests an einem Produkt in einer logischen Abfolge durchzuführen. Bei diesen Tests werden Messungen mithilfe von Messinstrumenten vorgenommen. Die verwendete Hardware überträgt mithilfe von Software (Teststeuerung) an einen Computer. Gleichzeitig vergleicht die Software die Ergebnisse mit vordefinierten Grenzwerten, um festzustellen, ob ein Produkt den Test bestanden hat oder durchgefallen ist. Durch die Automatisierung kann das Testverfahren sehr schnell, zuverlässig und wiederholt durchgeführt werden, wobei das Risiko menschlicher Fehler eher gering ist. Automatisierte Tests werden heute in allen Branchen eingesetzt, in denen Elektronik verwendet wird Gleichzeitig steigt die Anzahl automatisierter Tester zurzeit erheblich.
Alltägliche Beispiele für automatisierte Tests
Ein alltägliches Beispiel für den Wechsel von manuellen zu automatisierten Tests findet sich in lokalen Autowerkstätten. Als Autos noch einfach zu reparieren waren, brachten die Autofahrer sie zu einem Mechaniker, der Dinge wie den Verteiler, die Zündkerzen und die Kraftstoffzufuhr zum Vergaser manuell prüfte. Diese Kontrollen wurden nacheinander durchgeführt, bis der Fehler diagnostiziert und die Reparatur durchgeführt wurde. Heutzutage schließt der Mechaniker das Fahrzeug an einen Computer an, drückt eine Taste und analysiert dann die Testergebnisse, die der Computer nach einer Reihe umfassenderer Messungen liefert. Bei der Prüfung eines Motorsteuergeräts (ECU – Engine Control Unit) beispielsweise werden viele Tests durchgeführt, ohne dass der Mechaniker überhaupt wissen muss, was genau passiert. Dieser Prozess wird als automatisierter Test definiert, bei dem eine Reihe von Tests an einem Produkt nacheinander durchgeführt wird.
Die Geschichte automatisierter Tests
Produkte sind unterschiedlich komplex, und das gilt auch für die Art und Weise, in der sie getestet werden müssen. Je komplexer ein Produkt ist, desto teurer ist oft seine Herstellung und Prüfung. Automatisierte Testausstattung (ATE – Automated Test Equipment) wird während des gesamten Produktentwicklungszyklus eingesetzt: von der Entwicklung des ersten Prototyps über die ersten Batch-Tests bis hin zur vollständigen Produktion. Dieselben Testsysteme werden anschließend häufig in Reparaturwerkstätten oder bei Vertragsherstellern (CMs – Contract Manufacturers) eingesetzt). Unabhängig vom Produktionsstandort werden die Testgeräte in der Regel in der Nähe des Forschungs- und Entwicklungszentrums des Unternehmens konzipiert und entwickelt. Dies soll es den Ingenieuren ermöglichen, erste Ideen darüber auszutauschen, wie ein Produkt am besten geprüft werden kann, und eine kosteneffiziente Lösung zum Testen des Produkts zu erarbeiten.
In vielen Fällen installieren die Testentwicklungsingenieure die Geräte und schulen die Bediener vor Ort darin, wie sie die Geräte verwenden müssen, um eine maximale Leistung zu erzielen. Die Entscheidung über die zu verwendenden Testaustattungen wird im Allgemeinen anahnd des Produkts gefällt, das hergestellt werden soll. In der Vergangenheit waren ATEs teuer und schwer zu programmieren. Sie wurden in erster Linie für unternehmenskritische Produkte verwendet. Bei den frühen Testausstattungen handelte es sich um rack-basierte Testsysteme, deren Racks mit Einzelinstrumenten vollgepackt waren. Die Instrumente wurden häufig über einen General Purpose Interface Bus (GPIB) miteinander verbunden, der in den 1960er Jahren von Hewlett-Packard entwickelt wurde. Der GPIB ist ein paralleler 8-Bit-Bus, der den Vorteil bot, dass Systementwickler jede einzelne Komponente der Messinstrumente über ein einzigartiges und intuitives Adressierungssystem ansteuern konnte. So konnten Softwareentwickler entscheiden, welche Instrumente in welcher Reihenfolge angesteuert werden und wann die Testergebnisse zurückgegeben werden. GPIB war eine revolutionäre Neuerung bei der Entwicklung von Testsystemen und ist auch heute noch weit verbreitet.
Testausstattung hat in den letzten drei Jahrzehnten eine sprunghafte Entwicklung erlebt: schnellere Busse wie PCI, PCI Express, PXI, Ethernet, USB und anderes mehr. Diese neuen Standards ermöglichen eine deutlich schnellere Übertragung von Daten zwischen den Instrumenten der Testausstattung und dem Computer. Infolgedessen sind die Kosten für automatisierte Testausstattung erheblich gesunken und die Leistung stark gestiegen. Voll funktionsfähige ATE-Geräte kosten heute nur noch einige Tausend Euro im Vergleich zu Hunderttausenden in den 1980er Jahren und früher. Angesichts der sinkenden Preise und der technologischen Verbesserungen hat sich der Einsatz von ATEs überall in den Unternehmen verbreitet. Einst waren ATE-Systeme nur der Prüfung unternehmenskritischer Produkte vorbehalten, heute sind sie in den meisten High-Tech-Fertigungsunternehmen, üblich, die eine Reihe von Produkten herstellen, von preisgünstigen bis hin zu hochwertigen.
Manuelles Testen vs. automatisiertes Testen
Manuelle Testverfahren werden normalerweise von einer oder mehreren Personen durchgeführt. Diese Personen erledigen eine Messaufgabe nach der anderen, bis die Prüfung abgeschlossen ist. Sehr häufig haben Unternehmen Bediener eingestellt, die den ganzen Tag vor den Testgeräten sitzen, die Instrumente beobachten und die Testergebnisse aufschreiben. Dieses Verfahren wird seit vielen Jahren angewandt und wird auch weiterhin eingesetzt, wenn die Arbeitskosten niedrig sind. Manuelle Tests erfolgen auch dann, wenn das Testen eines Produkts relativ einfach ist und ein Bediener die Tests in kurzer Zeit durchführen kann. Bei automatisierten Tests hingegen übernimmt ein computergestütztes Testsystem das Verfahren zum Testen eines Produkts. Früher war automatisierte Testausstattung kostspielig und kompliziert. Die meisten automatisierten Testsysteme wurden für das Verteidigungswesen sowie die Automotive- und die Telekommunikationsbranche gebaut. Von den 1970er bis zu den frühen 1990er Jahren waren die Kosten für Computer im Verhältnis zu den Arbeitskosten extrem hoch. In dieser Zeit überstiegen die Kosten für automatisierte Testausstattung die Arbeitskosten bei weitem. Daher waren manuelle Tests immer noch vorherrschend.
Testsequenzen und Software zum Ausführen von Tests
Einzelne Tests (als Testmodule bezeichnet) führen bestimmte Funktionen und Überprüfungen durch. Wenn diese einzelnen Tests zusammengefügt werden, ergibt sich daraus eine sog. Testsequenz. Ein Beispiel für eine Testsequenz wäre (1) ein Einschalttest, gefolgt von (2) einem Spannungstest, gefolgt von (3) einem Stromtest. Bei automatisierter Testausstattung können mehrere Testsequenzen erstellt werden, um die Prüfung vieler Produkte innerhalb desselben Systems zu ermöglichen. Testmodule können in vielen Programmiersprachen erstellt werden, wohingegen Testsequenzen üblicherweise mit einem Tool zum Durchführen von Tests erstellt werden. Ein derartiges Tool besitzt viele Funktionen, einschließlich der Erstellung individueller Testsequenzen sowie der Integration von Messgrenzen, um zu bestimmen, ob ein Test bestanden wurde oder fehlgeschlagen (Pass/Fail) ist. Außerdem werden Bedingungen definiert, unter denen neue Testsequenzen auf der Grundlage der Messungen aufgerufen werden können. Diese Art von Software bildet auch einen Rahmen für die Ausgabe von Testdaten, sodass die Ergebnisse zur weiteren Analyse in Datenbanken hochgeladen werden können.
Halbautomatische Tests
Bei der Abwägung zwischen manuellen und automatisierten Tests ist es wichtig, nicht in Schwarz-Weiß-Denken zu verfallen. Viele Unternehmen nutzen eine dritte Option für ihre Teststrategie, sogenannte halbautomatische Tests. Diese Option kommt in der Regel zum Einsatz, wenn das Produkt während der Prüfung in irgendeiner Form konfiguriert werden muss. Bei einem halbautomatischen Test ist ein Bediener zumindest während eines Teils des Testzyklus anwesend. Das Produkt wird in der Regel in einer Vorrichtung platziert, die mit einem Computer verbunden ist. Während des Testverfahrens führt eine grafische Benutzeroberfläche (GUI) auf dem Computerbildschirm den Bediener durch die Teile des Testverfahrens, die eine manuelle Anpassung des Produkts erfordern. Dies kann das Einstellen eines Potentiometers oder das Ausrichten eines bestimmten mechanischen Teils bedeuten. Der Computer kann einen Parameter ablesen, während der Bediener die Anpassungen vornimmt. Sobald der Wert innerhalb des erforderlichen Bereichs liegt, kann der Computer den Bediener darauf hinweisen, dass er korrekt eingestellt wurde. Sobald diese Tests durchgeführt wurden, übernimmt der Computer wieder die Arbeit und die restlichen Tests erfolgen auf dieselbe Weise wie zuvor beschrieben vollautomatisch.
Typen automatisierter Tests
Automatisierte Testsysteme gibt es in allen Formen und Größen. Hier finden alle Kompetenzbereiche Anwendung: Optik, RF, Mechanik, Elektrik und Elektronik, Software und weitere Fachgebiete, die alle an verschiedenen Stellen der unterschiedlichen Testprojekte erforderlich sind.
Einige Beispiele für Testtypen sind:
- In-Circuit-Test
- Boundary-Scan
- Automatische optische Inspektion (AOI)
- Automatische Röntgeninspektion (AXI – Automated X-Ray Inspection)
- Automatisierte Testausstattung für Funktionstests
- Kombinierter Test
In-Circuit-Test (ICT)
In-Circuit-Tests gibt es schon seit vielen Jahren. Ursprünglich dienten sie zur Prüfung einzelner Leiterplatten, die in elektronische Produkte eingebaut wurden. Eine elektrische Sonde prüft eine bestückte Leiterplatte (PCB) auf Kurzschlüsse, offene Schaltungen, Widerstand, Kapazität und andere grundlegende Elemente, die zeigen, ob die Baugruppe korrekt hergestellt wurde. Die Prüfung kann mit einem "Nagelbett"-Werkstückträger und spezieller Testausstattung oder mit einer In-Circuit-Testkonfiguration ohne Werkstückträger durchgeführt werden. Bei einem Tester mit Nagelbett handelt es sich um eine elektronische Vorrichtung, die zahlreiche Stifte enthält, die in Öffnungen in einer mit Glasgewebe laminierten Platte eingesetzt sind. Die Stifte werden mithilfe von Werkzeugstiften so ausgerichtet, dass sie mit Testpunkten auf einer Leiterplatte in Kontakt kommen. Die Testpunkte werden wiederum über Drähte und Kabel mit einer Messeinheit verbunden. Jeder der kleinen, federbelasteten Stifte stellt den Kontakt zu einem Knoten in der Schaltung des Prüflings (DUT – Device under Test) her. Indem der Prüfling gegen das Nagelbett gedrückt wird, kann schnell und gleichzeitig ein zuverlässiger Kontakt zu Hunderten oder sogar Tausenden von einzelnen Testpunkten innerhalb der Schaltung des Prüflings hergestellt werden. Die Niederhaltekraft kann manuell oder durch ein Vakuum erzeugt werden, wodurch der Prüfling nach unten auf die Nägel gezogen wird. ICT-Systeme verfügen häufig über eine eingebaute Testdatenprotokollierung mit herstellereigenen Ausgabeberichten, die auf dem Design des Herstellers basieren. Auch heute sind noch viele ICT-Systeme im Einsatz, obwohl sie allmählich von den Boundary-Scan-Systemen abgelöst werden, die weiter unten beschrieben werden. ICT-Tests bieten viele Vorteile, wie z. B. die hohe Prüfgeschwindigkeit und die Möglichkeit, viele Teile der Leiterplatte gleichzeitig zu prüfen. Außerdem sind sie in standardisierter Form im Handel erhältlich. Sie werden in der Regel verwendet, um bestückte Einzelplatinen zu testen, bevor sie in Unterbaugruppe integriert werden.
Boundary-Scan
Boundary-Scans sind eine Form automatisierter Tests, die sich seit einigen Jahren großer Beliebtheit erfreut. Boundary-Scans sind auch unter der Abkürzung JTAG (Joint Test Action Group) oder unter ihrem IEEE-Standard (IEEE 1149.1) bekannt. Sie bieten viele entscheidende Vorteile gegenüber traditionelleren Testformen. Daher haben sie sich in der heutigen Zeit zu einem der wichtigsten Werkzeuge für automatisierte Tests entwickelt. Der Hauptgrund für die Entwicklung von Boundary-Scan-Tests bestand ursprünglich darin, bei Tests den mangelnden Zugang zu Platinen und integrierten Schaltungen zu beheben. Da die Produkte immer kleiner wurden, wurde der verfügbare Platz immer knapper, sodass herkömmliche Testmethoden sich nicht mehr eigneten. Boundary-Scans schaffen hier Abhilfe, indem spezielle Boundary-Scan-Register in großen integrierten Schaltkreisen auf der Leiterplatte angebracht werden. Wenn die Karte auf Boundary-Scan-Modus eingestellt ist, werden Daten an serielle Datenregister in den integrierten Schaltkreisen weitergeleitet. Die Antwort und damit die Daten, die aus dieser seriellen Datenkette übermittelt werden, ermöglichen es dem Tester, Fehler mit relativ hoher Geschwindigkeit zu erkennen. Aufgrund ihrer Fähigkeit, Platinen und sogar integrierte Schaltkreise mit sehr begrenztem physischem Testzugang zu prüfen, sind Boundary-Scans inzwischen weit verbreitet und ihr Einsatz nimmt weiterhin zu.
Automatische optische Inspektion (AOI)
AOI ist in vielen Fertigungsumgebungen üblich. Es handelt sich im Grunde um eine Form der Sichtprüfung, die jedoch automatisch mit Kameras, Computern und Software erfolgt. Aufgrund des automatisierten Charakters der Inspektion bietet sie im Vergleich zur traditionellen manuellen Inspektion ein wesentlich höheres Maß an Wiederholbarkeit und Geschwindigkeit. Die AOI ist besonders nützlich, wenn sie am Ende einer Produktionslinie steht, in der gelötete Leiterplatten hergestellt werden. Dort können Produktionsprobleme, einschließlich Lötfehler, schnell lokalisiert werden, und es kann festgestellt werden, ob die richtigen Komponenten in der korrekten Ausrichtung eingebaut wurden. Diese Art der Inspektion wurde traditionell von Bedienern durchgeführt, die sich dieselbe Art von Leiterplatten über einen Zeitraum von mehreren Stunden ansahen. Eines der größten Probleme bei der manuellen Sichtprüfung ist die Ermüdung des Bedieners. Gegen Ende einer Schicht lässt die Genauigkeit der manuellen Prüfung oft nach. Das führt dazu, dass schlechte Produkte passieren oder gute Produkte durchfallen. Mit AOI werden diese Probleme erfolgreich angegangen. Aufgrund der hohen Kosten von AOI-Systemen werden sie oft nur in Produktionslinien mit hohen Stückzahlen eingesetzt.
Automatische Röntgeninspektion (AXI – Automated X-Ray Inspection)
AXI hat große Ähnlichkeiten mit AOI. Mit dem Aufkommen von BGA-Gehäusen (Ball Grid Array) war es jedoch notwendig, eine Form der Inspektion zu schaffen, die die Sichtung von Elementen ermöglicht, die optisch nicht sichtbar sind. AXI-Systeme können durch IC-Gehäuse (Integrated Circuit) hindurchsehen, um die Lötstellen genau zu beurteilen, so wie ein Arzt ein Röntgenbild eines Knochens betrachtet, um eine mögliche Fraktur zu erkennen.
Automatisierte Ausstattung für Funktionstests
Bei Funktionstests wird – wie der Name schon sagt – die Funktionalität von Geräten getestet. Funktionstests erfolgen deutlich später im Herstellungsprozess. Häufig handelt es sich um den letzten Test, bovor das Produkt verpackt und an den Kunden geliefert wird. Sobald ein Produkt diese Testphase erreicht hat und sich dabei ein Fehler herausstellen sollte, ist die Reparatur in der Regel am teuersten. Je früher ein Problem oder ein Konstruktionsfehler bei einem Test erkannt wird, desto kostengünstiger ist die Lösung des Problems. Der Großteil der Funktionstester muss kundenspezifisch angefertigt werden, da die meisten Funktionen der Produkte eines Unternehmens spezifisch für das jeweilige Unternehmen sind. Wenn ein neues Produkt konzipiert und hergestellt wird, verfügt es häufig über Funktionen, die es vorher noch nie gab. Das bedeutet, dass bis zu diesem Zeitpunkt noch niemand einen Tester für diese Funktionen gebaut hat.
Kombinierte Tests
Wie Sie anhand der bereits besprochenen Testarten sehen können, kann keine einzelne Testmethode eine vollständige Lösung bieten. Um diesem Problem zu begegnen, werden in vielen ATE-Systemen verschiedene Testmethoden in einem Tester kombiniert. Durch die Kombination der Testfunktionen ist die Testabdeckung wesentlich höher. Ein kombinierter Tester kann auch eine Vielzahl verschiedener Testarten durchführen, ohne dass der Prüfling physisch von einem Tester zum anderen bewegt werden muss. Diese einzelne Testsuite kann sowohl ICT-Tests als auch Funktionstests und Boundary-Scan-Tests (JTAG) umfassen. Jede der beschriebenen Arten von automatisierten Tests hat ihre Stärken. Daher ist es notwendig, den jeweils richtigen Testansatz für die erforderlichen Tests zu wählen. Durch die Kombination der verschiedenen verfügbaren Testtechniken ist es möglich, dass jede gebaute ATE optimal genutzt werden kann. Auf diese Weise lassen sich Test zeitsparend durchführen. Gleichzeitig stellt dies einen hohen Abdeckungsgrad für die erfolgreiche Prüfung aller Produkttypen sicher.
Entscheidung zwischen manuellen und automatisierten Tests
Wenn ein Unternehmen sich den Verwendungszweck eines Produkts komplett vor Augen führt und gleichzeitig das Fertigungsvolumen berücksichtigt, ergibt sich der richtige Weg im Allgemeinen automatisch. Häufig werden unternehmenskritische Produkte mehrfach getestet, um ihren korrekten Betrieb sicherzustellen. Beispiele für derartige Produkttypen sind solche Produkte, die der Sicherheit von Menschen dienen oder bei denen eine fehlerhafte Funktionsweise katastrophale Folgen haben könnte, z. B. Produkte in den Branchen transportation, Luft- und Raumfahrt, Medizin und and Verteidigungswesen. Unternehmen, die Flugzeugkomponenten herstellen, wissen beispielsweise, dass jeder Fehler in ihren Produkten zu Todesfällen und Zerstörung in großem Umfang führen kann. Aus diesem Grund investieren diese Unternehmen stark in automatisierte Testausstattung. Ein anderes Beispiel sind Hersteller von implantierten medizinischen Geräten. Die Produktqualität kann hier über Leben und Tod des Anwenders entscheiden.Unternehmen wie diese haben schon früh aus Sicherheits- und Kostengründen auf automatisierte Testtechnologie gesetzt.. Automatisierte Tester werden nie müde und haben keine schlechten Tage. Wenn ein Bediener die erforderlichen Aufgaben erledigt, können die Ergebnisse nachweislich variieren, je nachdem ob sie vor oder nach dem Mittagessen erfasst wurden. Außerdem kann Subjektivität hier eine Rolle spielen. Was für ein Person geeignet erscheinen mag, ist es für eine andere Person möglicherweise nicht. Produkte, die nicht auf den Markt hätten gelangen sollen, sind trotzdem dort angekommen, und Artikel, die zurückgewiesen wurden, haben sich als völlig einwandfrei herausgestellt. Derartige Fehler verursachen hohe Kosten durch Rückrufaktionen, Reparaturen und Imageschaden. Bei der Verwendung objektiver Grenzwerte sind die Ergebnisse immer verlässlich und reproduzierbar.
Eignet sich das Anwendungsfeld für Automatisierung?
Manuelle Tests werden traditionell eingesetzt, wenn es sich um einen einfachen Prozess handelt und die Arbeitskosten niedrig sind. Manuelle Tests werden häufig auch in Forschungs- und Entwicklungsabteilungen eingesetzt, wo Flexibilität einen wichtigen Faktor darstellt, wenn neue Produkte getestet werden, die sich noch in der Entwicklungsphase befinden. Die Möglichkeit, einen Testprozess zu ändern und verschiedene Optionen auszuprobieren, spricht für manuelle Tests. Unternehmen fällt es bisweilen schwer, von einem manuellen Testverfahren auf ein automatisiertes Testverfahren umzusteigen, da die Kosten für die Softwareentwicklung hoch erscheinen können.
Da die Kosten für Testgeräte und Softwaretools im Einklang mit dem Mooreschen Gesetz sinken, werden automatisierte Tests heutzutage in großem Umfang für die Prüfung aller Arten von elektronischen Produkten eingesetzt. In dem Maße, wie die Kosten für Testausstattung sinken, breitet sich der Einsatz von automatisierter Testausstattung immer weiter aus. Ein weiterer Faktor, der zur Ausbreitung automatisierter Tests beiträgt, sind die weltweit steigenden Arbeitskosten, die die Kosten manueller Tests immer weiter steigen lassen. In Nischenbranchen, die spezielle Fertigkeiten erfordern, kann es außerdem schwierig sein, das richtige Personal zu finden und zu schulen. Automatisierte Tests werden über alle Produkttypen hinweg verwendet. Dies gilt unabhängig davon, ob es sich um kostengünstige Produkte mit hoher Stückzahl oder hochwertige Produkte mit niedriger Stückzahl handelt. Die Faktoren für die Entscheidung, welche Testausstattung verwendet werden sollte, sind vom Typ der herzustellenden Produkte abhängig. Bei kostengünstigen Produkten mit hoher Stückzahl sind häufig sind die Testzeiten häufig der kritische Faktor: Die Einsparung von wenigen Sekunden kann den Ausschlag dafür geben, welche Art von Testausstattung verwendet wird. Bei komplexeren hochwertigen Produkten ist es wichtiger, dass viele tiefgreifende Tests durchgeführt werden können. Daher tendiert die Testausstattung dazu, einen höheren Entwicklungsstand aufzuweisen und höhere Kosten zu produzieren.
Ist die Automatisierung die Investition wert?
Eine der wichtigsten Entscheidungen, die Führungskräfte treffen müssen, wenn sie mit der Einführung eines neuen Produkts beginnen, ist die Entscheidung, ob sie in automatisierte Tests investieren sollen. Die Kosten für die Einrichtung eines automatisierten Testsystems sind zwar in den letzten Jahren gesunken, stellen aber immer noch eine erhebliche Investition dar. Wenn die Erstinvestition jedoch einmal getätigt ist, gibt es Möglichkeiten, sie in eine kostensparende Plattform zu verwandeln. Durch den Entwurf und die Implementierung von Teststationen mit einem gemeinsamen Kern können diese leicht wiederverwendet und in der gesamten Fertigung wiederverwertet werden. Der Schlüssel zu einem gemeinsamen Kern oder einer generischen Teststation liegt darin, die gesamte kostenintensive Instrumentierung in einer Basiseinheit zu gruppieren. Von dort aus ist es einfach, flexible Vorrichtungen für unterschiedliche Produkte und Phasen des Produktlebenszyklus zu entwickeln, indem sie je nach Bedarf ein- und ausgebaut werden.
Widerstand gegen die Einführung automatisierter Testausstattung kann auch aus dem Unternehmen selbst kommen, da einige Mitarbeiter ihre Arbeitsplätze durch die Einführung neuer Technologien bedroht sehen. Diese gefühlte Bedrohung wird häufig durch die Erkenntnis entkräftet, dass die Routineaufgaben durch spannendere Aufgaben ersetzt werden, die außerdem einen größeren Mehrwert für das Unternehmen schaffen können. Mit dem richtigen Einfühlungsvermögen lässt sich diese Situation in eine positive Erfahrung für alle Beteiligten verwandeln.
Die Hauptunterschiede zwischen manuellen, halbautomatischen und automatisierten Tests wurden bereits angesprochen, aber es bleibt die Frage, wie sich die richtige Entscheidung treffen lässt.
Um herauszufinden, welche Strategie für eine bestimmte Situation am besten geeignet ist, muss eine Reihe von Fragen beantwortet werden:
- Handelt es sich um ein kostengünstiges oder ein hochwertiges Produkt?
- Wird das Produkt in hoher Stückzahl gefertigt?
- Sind die Produkttests komplex oder relative einfach?
- Ist das Produkt für den Endkunden geschäftskritisch?
- Müssen 100 % der Einheiten geprüft werden oder reicht eine Chargenprüfung?
Die Antworten auf diese Fragen gestatten fundiertere Entscheidungen darüber, ob automatisierte Tests als neue Strategie eingeführt werden sollten. Bei Unternehmen, die kostengünstige und einfache elektronische Produkte herstellen, sind automatisierte Tests unerlässlich, um die Kosten für Herstellung und Prüfung niedrig zu halten. In diesen Fällen ist es viel zu kostspielig, wenn ein Bediener jedes Produkt von Hand prüft. Bei komplexen und hochwertigen Produkten ist es oft sinnvoll, die Prüfung zu automatisieren, da die Arbeitskosten für speziell ausgebildete Techniker, die für die Prüfung der komplexen Produkte benötigt werden, hoch sind. Die Kunden für hochwertige Produkte erwarten häufig ein hohes Testniveau und dokumentierte Prozesse, um eine gleichbleibende Qualität sicherzustellen. Bei unternehmenskritischen Produkten sind hohe Qualität und wiederholte Tests in allen Produktionsphasen ein absolutes Muss. Die Tests müssen in jeder Stufe der Montage durchgeführt werden – von der Prüfung der einzelnen Leiterplatten über die Prüfung der Teilsysteme bis zur abschließenden Funktionsprüfung für die Abnahme. Sollten diese Arten von Produkten im praktischen Einsatz versagen, sind die Kosten (d. B. die Kosten schlechter Qualität) deutlich höher als die Kosten für umfassende Tests.
Um die Unterschiede zwischen den angesprochenen Testprozessen besser zu verstehen und die Investitionen entsprechend zu rechtferigen, ist es hilfreich, ein Beispiel für ein typisches Testszenario heranzuziehen. In dem oben beschriebenen Testszenario werden für ein Produkt, das getestet werden muss, die potenziellen Kosten pro Test für jedes der drei Testverfahren aufgeschlüsselt. Die kritischen Berechnungsfaktoren, die sich auf die Entscheidung für die beste Strategie auswirken, sind die Testdauer, die Kosten für den Bediener, die Kosten für die Ausstattung und die erforderliche technische Entwicklung (d. h. das Softwaredesign). Im Beispiel wird davon ausgegangen, dass mit einer Fertigungslinie 10.000 Produkteinheiten pro Jahr entsprechend den geschätzten Fixkosten, den Entwicklungskosten und den Testzeiten hergestellt werden. Diese Informationen dienen als Berechnungsgrundlage für die Testkosten pro Einheit. Der kritische Kostenpunkt in diesem Beispiel ist die Testdauer. Je kürzer sie ist, desto drastischer sinken die Kosten pro Test.
Bei der manuellen Prüfung sind die Bedienerkosten höher, da er über höhere Kompetenz verfügen muss. Die Tests erfordern einen geschulten Testtechniker. Dies ist bei halbautomatischen oder vollautomatischen Testszenarios nicht der Fall. Hier kann ein weniger qualifizierter Bediener eingesetzt werden. (In diesen Fällen könnte der Bediener möglicherweise mit mehreren Testern gleichzeitig arbeiten, aber diese Multiplexing-Annahme wird bei diesen Berechnungen nicht berücksichtigt.) Das Beispiel in der Tabelle oben dient als Richtschnur, um die Kosten der unterschiedlichen Testszenarios zu berechnen. In diesem Fall rechtfertigt die Stückzahl (10.000 pro Jahr) den Wechsel von manuellen Tests zu halbautomatischen Tests, aber nicht die Umstellung auf vollautomatische Tests. Das liegt darin begründet, dass die Stückzahl hoch genug ist, um eine gewisse Form der Automatisierung zu rechtfertigen, durch die die Arbeitskosten deutlich gesenkt werden. Die Stückzahl ist aber nicht hoch genug, um die noch höheren Kosten einer vollständigen Automatisierung zu rechtfertigen.
Erfolgreiche Produkttests sind entscheidend für die Qualität, aber sie sind mit Kosten verbunden. Bei der Entscheidung, ob Produkttests manuell oder automatisiert erfolgen sollen, müssen die oben genannten Aspekte sorgfältig abgewogen werden. Eine gute Planung führt zu effektiven Ergebnissen und beschleunigt die Fertigung. Gleichzeitig wird das Gesamtergebnis verbessert.
Hier finden Sie Informationen zu ergänzenden Themen:
Machine Vision & Optische Inspektion - Montage mit aktiver Ausrichtung - Testtechnikexpertise - RF-Testinstrumentierung - Smartes Datenmanagement