Automation is Key to Quality and Safety
In the fast-paced and highly regulated medical and pharmaceutical industries, ensuring the quality and safety of products is crucial. A critical aspect of this process is the testing and inspection of the product’s primary packaging. These units are the only barrier between a person’s body and the treatment they need. Defective packaging can lead to contamination, which can result in long-term repercussions. While durability and functional material testing (which can include tear and puncture resistance, stress testing and other handling processes) is a primary consideration, this article explores the challenges and advantages in medical packaging inspection.
While packaging may seem like an afterthought to those outside the medical field, it must also undergo strict compliance requirements and acquire approval from agencies such as the FDA, EMA, etc. For example, producing medication is a very sophisticated chemical balance and is significantly affected by environmental factors like shape, size, temperature, etc. Additionally, many life-saving devices like stents are stored in sterile pouches to avoid outside particles and bacteria. The consequences from a contaminated implant last for decades.
The Inside Scoop on Medical / Pharma Packaging
There are three types of packaging that must be considered:
Primary Packaging Any material that comes in direct contact with the product. There are plenty of options here including pouches, vials, bottles, syringes, stoppers, blister packs, etc. |
Secondary Packaging Additional packaging that will contain the medication information, but never touches the product itself. A good example would be the box holding the blister pack. |
Tertiary Packaging This packaging is invisible to the end-user and protects the goods during the shipping process. |
There are materials that are more commonly used for pharmaceutical packaging, for different purposes. These materials are selected based on the specific requirements of the product, including protection from environmental factors, compatibility with the drug, and regulatory standards. In addition to glass (primary) and paper/cardboard (Tertiary), these can include:
Material |
Characteristics |
Application Examples |
Tyvek® |
Tyvek is a brand of high-density polyethylene fibers, a strong and durable synthetic material which is resistant to penetration. It is breathable which allows sterilization gases to penetrate while blocking bacteria and other contaminants. |
|
High-Density Polyethylene (HDPE) |
HDPE is a type of thermoplastic polymer made from petroleum. It is known for its high strength-to-density ratio, high chemical resistance and moisture barrier properties. |
|
Low-Density Polyethylene (LDPE) |
LDPE is a softer, more flexible form of polyethylene with a strong moisture barrier. |
|
Polyethylene Terephthalate (PET) |
PET is a strong, clear plastic with excellent barrier properties against moisture and oxygen. |
|
Polyvinyl Chloride (PVC) |
PVC is a versatile plastic with a high barrier against moisture, light, and oxygen. |
|
Laminates and coatings are also used to enhance the properties of these packaging materials. For example, multilayer films combine different materials to provide improved barrier properties, strength, and durability.
Challenges in Medical Packaging Inspection
Medical packaging inspection is very complex, and consistency is vital. The primary objective is to ensure that every package is free from contamination and defects, properly labeled and has a proper seal to guarantee the safety, sterility, and efficacy of the product. Common challenges that manufacturers face are :
1. Uncompromising Requirements and Regulatory Compliance
Medical packaging must meet stringent regulatory standards. Any deviation like incorrect labeling, damaged packaging, or contamination, can have severe consequences. From a business perspective, that can lead to product recalls and harm to a brand. From a real-world perspective, it can put patients in dangers.
Examples of Medical Packaging Inspection Requirements
Particles and Contamination |
Particles and Contamination within the Critical Area contained by the Weld Lines/Seal |
Folds and Imprints |
Unwanted Folds and/or Imprints |
Holes, Cuts and Damages |
Defects that Expose the Product and Impair its Disinfection and/or Sterilization |
Prints |
Printing Defects Found within a Predefined Print Area |
In-Line Prints |
Print Defects Found within a Predefined In-Line Print Area |
Container Closure Integrity Testing (CCIT) |
Ensure the contents of a container (like a pouch or bag) remain sterile and protected. |
Welding Issues |
All Issues on the Weld Line/Seal e.g., Weld Width, Uniformity, etc. |
Label Scanning |
Accurate Traceability Information for Each Unit |
Sterilization Verification Indicators |
Confirmation a Product has Passed the Sterilization Process |
Manufacturing Faults |
Examples: Cutting Position, |
2. Variety of Packaging Formats
There is a wide variety of packaging types, including pouches, overwrap bags, stoppers, blister packs, bottles and vials. Each format presents unique inspection challenges, requiring specialized inspection techniques.
3. Speed and Efficiency
In a high-volume production environment, speed and efficiency are critical. Traditional manual inspection methods can be time-consuming and prone to human error, making it difficult to maintain the required pace of production.
4. Specialized Labor
With medical products, even the smallest bubble, scratch or misprint can impose a major issue. To inspect these products manually, specialized expertise is required which can be hard to find, expensive and very difficult to replace. Regardless of the operator’s skill level, this can become a mundane task which often leads to errors and misjudgment.
Benefits of Automated Vision Inspection
Automated medical packaging inspection has emerged as a vital technology that addresses the challenges of traditional inspection methods. It has revolutionized medical packaging inspection by addressing these challenges and offering several significant benefits:
With the help of advanced lighting, automated vision inspection systems use cutting-edge imaging technologies, such as optical sensors, special light techniques, and high-resolution cameras. These can take hundreds of pictures in seconds, ready for analysis. Using specialized machine vision software, they can detect defects with unparalleled accuracy. These systems can identify even the smallest defects, ensuring that every package meets the highest quality standards. The results are always more consistent than human inspectors, fatigue, boredom and subjectivity are eliminated. They provide reliable and consistent inspection results, reducing the risk of defective products reaching the market.
Automated vision inspection systems operate at high speeds, delivering a high throughput with fewer false rejects. This efficiency helps manufacturers meet production targets and reduces bottlenecks in the packaging process. Additionally, they are not limited to one task. Automated systems can inspect various aspects of packaging, including label accuracy, seal integrity, quantity, defects/damage and the presence of foreign particles.
With this enhanced data, they can generate detailed documentation on inspection results, allowing manufacturers to analyze trends and identify recurring issues in addition to having a built-in paper trail. This simplifies documentation for regulatory compliance and helps make informed decisions to improve the overall process.
Human-Like Inspection in Manufacturing 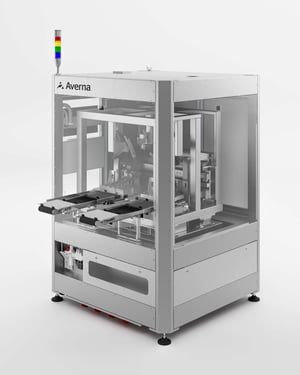
Human-like inspection refers to the integration of artificial intelligence (AI), machine learning (ML) and mechatronic technologies to accurately mimic human inspectors. There are times where human-like inspection capabilities are essential. This approach combines the best of both worlds – the precision of automated systems and the adaptability of human inspectors.
As an example, in the case of a medical pouch, human-like inspection is a true asset. A manual inspector will pick up the pouch and verify both sides by turning it over in different directions. They will use light to try to catch scratches at different angles. They will open the pouch to look for particles on the inside. These human-like actions leave no stone unturned.
Human-like inspection systems can also adapt to new defect types and packaging variations, making them more versatile and effective over time. People rely on what they know to make decisions. AI-powered systems can analyze factors like design, type, and historical results to make better educated decisions.
Conclusion
Automated packaging inspection is a game-changer in the industry, producing better products, higher throughput, and meeting compliance regulations faster. As the medical industry evolve, the adoption of automated inspection technologies will become increasingly important. Manufacturers that don’t invest in these technologies are certain to fall behind their competitors. The future of medical packaging inspection lies in the seamless integration of automated systems and human-like capabilities, creating a robust and reliable inspection process that guarantees the highest level of quality for medical products.
For more information about medical grade packaging and human-like inspection systems, please contact us.